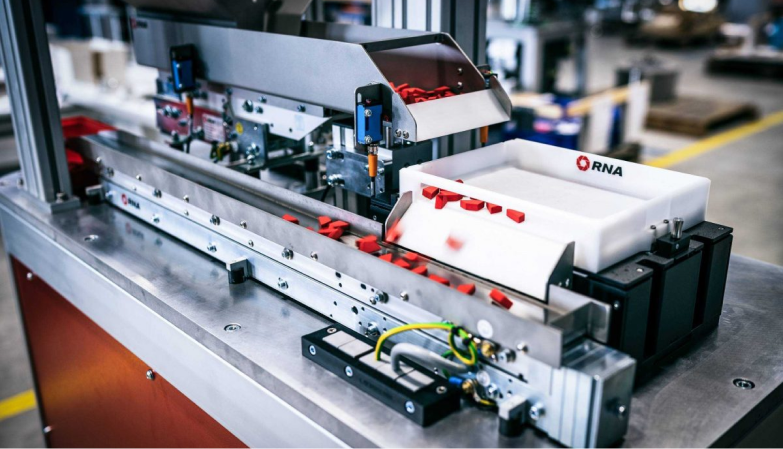
Vision feeding systems
focus on maximum quality and output
For deviating products and error-free output of small batches, a vision feeding system offers the solution. Unlike mechanical feeding systems, which often operate more roughly, digital feeding technology excels in flexibility and precision. Using cameras and sophisticated software, a vision system records the position and orientation of individual items and can precisely determine the quality and speed of the feed flow.
Vision feeding systems: you don't know what you see
A vision feeding system basically works the same as a traditional feeding system. Here, too, the process starts by dumping loose products into a shaker. Shaking and vibrating move the products apart so that they can be further processed one by one. In a mechanical infeed system, the items then pass through a linear module to a singulator before arriving at the manipulator, but a vision system skips all those steps. A camera detects the exact position of each individual item and then transmits the coordinates for further processing. Determining orientation and positioning accurately is lightning-fast and essential for error-free output.
Vision feeding systems vs traditional feeding systems
The main difference between a traditional feeding system and a vision feeding system is that you can do much more. The main advantage of a digital feeding solution is that you are much more flexible and can also work more precisely. Traditional systems, such as the bowlfeeders we develop at Special Machinery Netherlands, are made to feed a wide variety of products. From uniform items to complex parts, everything can basically be processed, except that not all materials are suitable for feeding via a bowlfeeder. Silicone and rubber products, for example, can cause a mechanical bowlfeeder to jam. Vision feeding systems are less sensitive to geometric tolerances and do not have this problem.
Digital feeding solutions, on the other hand, have hardly any limitations. Whatever the product characteristics or dimensions, a vision system is able to quickly scan products and determine their position, and this makes them ideal for a wide range of applications, from small delicate items to larger, irregularly shaped products.
Three vision solutions for the manufacturing industry
At Special Machinery Netherlands, we have positioned ourselves as a premier provider of robust feeding systems. Our extensive knowledge and years of experience in bowlfeeders distinguish us in the Netherlands. Furthermore, we are proficient developers of digital feeding systems. To ensure the best solution, we choose from three existing vision systems, each with its own unique benefits and applications:
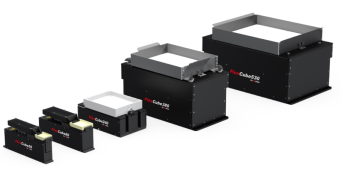
Flexcube
The FlexCube® offers a flexible solution for hard-to-orient products and fragile materials. Available in various sizes and equipped with proprietary machine vision systems, the FlexCube® capable of handling multiple product types simultaneously. This makes it particularly suitable for complex production lines where fast switching between different products is required.
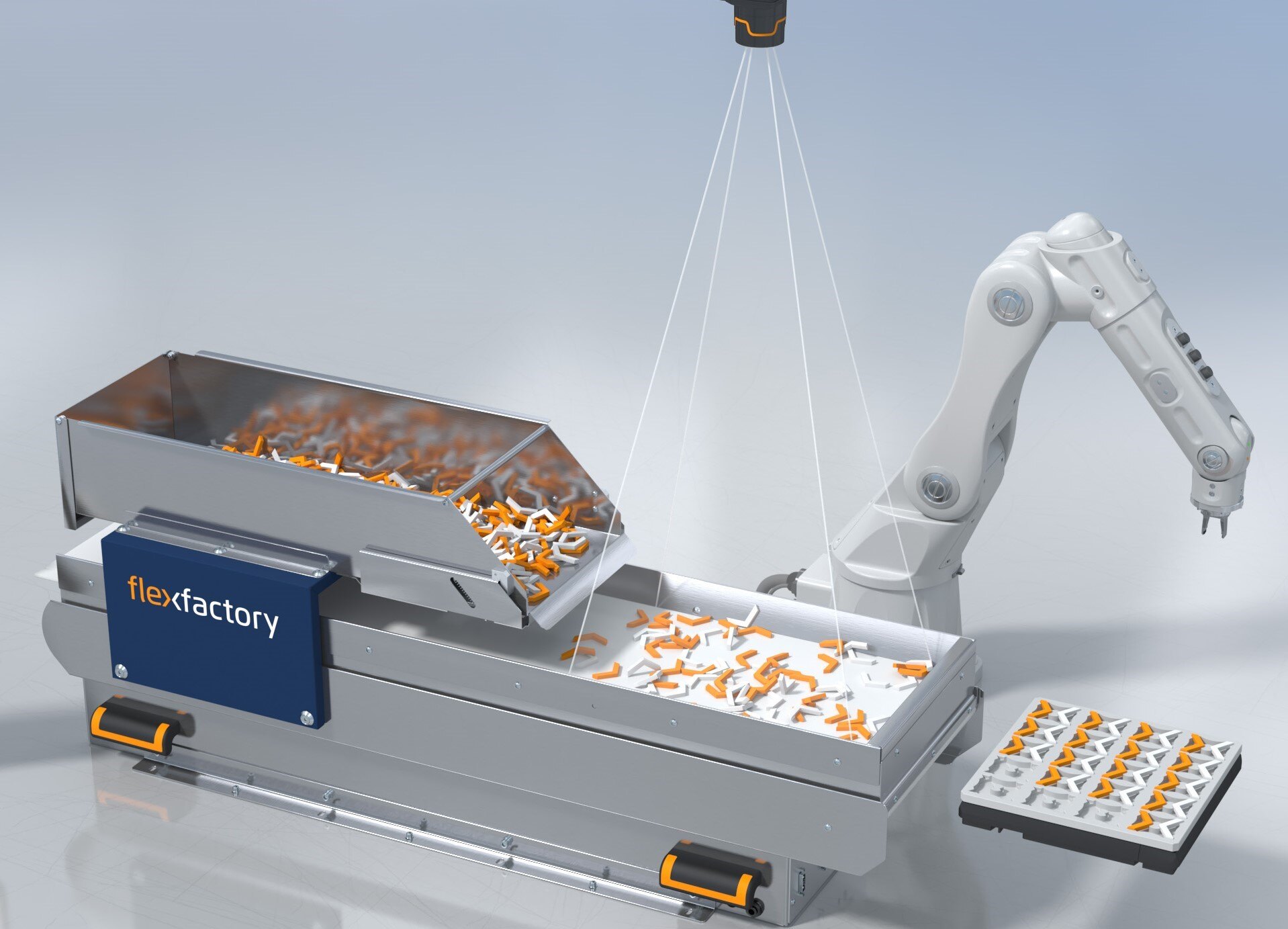
AnyFeed
The AnyFeed is a flexible solution for bulk feeding. It quickly recognizes components of different sizes, shapes, and materials using 3D cameras, allowing users to easily switch production scenarios. The combination of high-resolution vision technology with robotics makes the system widely applicable across various industries.
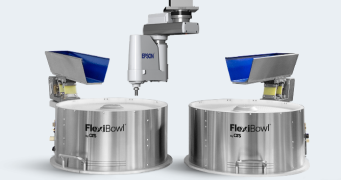
Flexibowl
This platform is ideal for efficient feed processing. The FlexiBowl is designed to perform independent and simultaneous process steps, allowing multiple products to be processed simultaneously and ensuring high output. Highly expandable and running on user-friendly software, the FlexiBowl is an excellent choice for flexible and future-proof feed solutions.
Benefits of robotic vision feeding systems
Although vision feeding systems are more expensive than traditional ones, they offer significant advantages. Not only are they more versatile, but systems with camera technology can also transition between different product batches more swiftly. Furthermore, vision systems can be effortlessly upgraded with simple software updates and continuously improved with AI technology.
Digital feeding systems guarantee maximum flexibility and minimal risk of failure, both now and in the future. In contrast to mechanical bowlfeeders, which can lead to product pinching, digital feeding technology ensures a seamless, error-free product flow.
Flexible
Faster gear changes
Easy to expand
Lower error margins
Expertise in hardware en software
Special Machinery Netherlands is known for building unique and robust bowlfeeders. We supply mechanical feeding systems of proven top quality and we also have a knack for digital solutions.
We use the best vision technology available on the market, just like our competitors, but what sets us apart is the added value we offer. With our long experience in traditional feeding technology, we are uniquely able to combine modern camera systems with proven bunker systems and other mechanical solutions, and can guarantee robust and consistent output.
The expertise of our programmers combined with the craftsmanship of our bowlfeeders guarantees a working total solution and the most efficient production line.
Seeing is believing
At Special Machinery Netherlands, we create feeding systems that can withstand any level of scrutiny. We don't just claim this; we can prove it. All the solutions we develop are first tested for feasibility in our own testcenter. Only when we are confident we can deliver on our promises do we begin construction.
All the machines we build, both mechanical and vision systems, undergo strict quality control. As part of our factory acceptance test (FAT), each system must operate flawlessly for a minimum of four hours, during which we carefully ensure that the requested output is consistently delivered.
Email or call us for more information, or schedule an appointment to see for yourself what our vision feeding solutions are capable of.
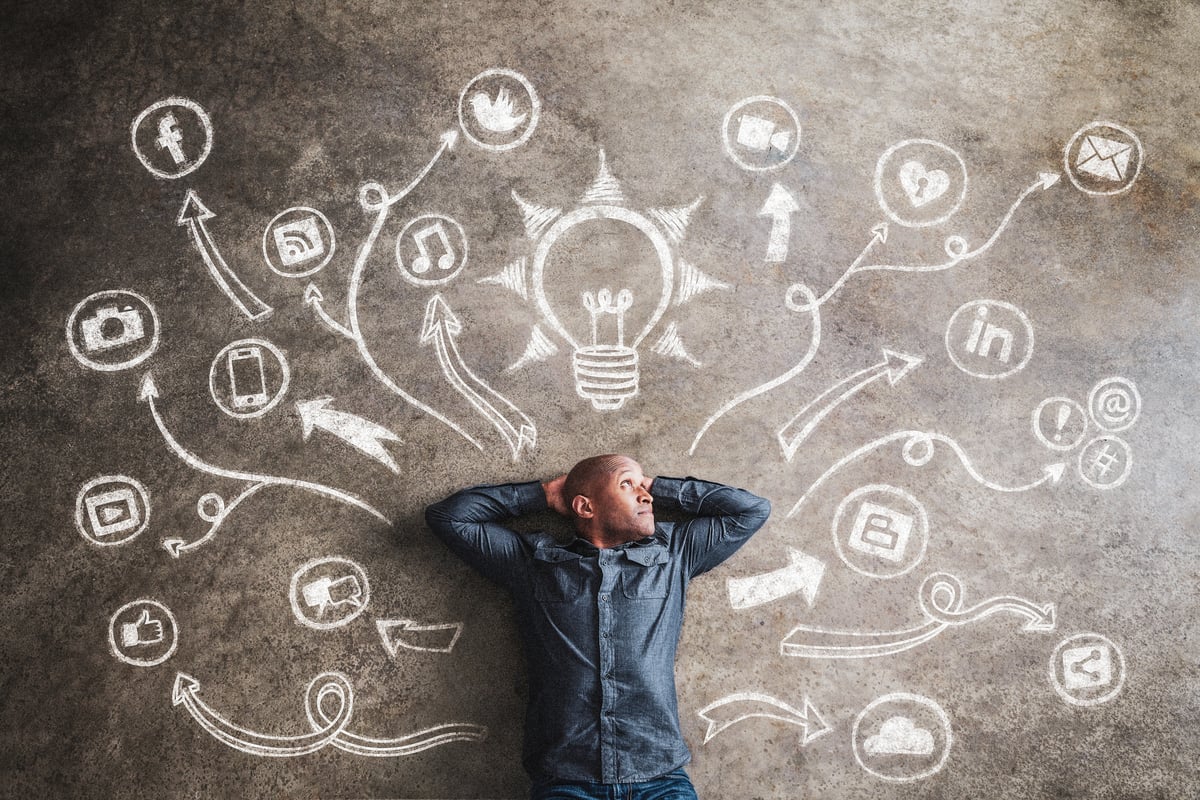
Together we create the future of manufacturing
Our experienced engineers work closely with you to understand your unique challenges. We design and build customized machines that perfectly match your processes.