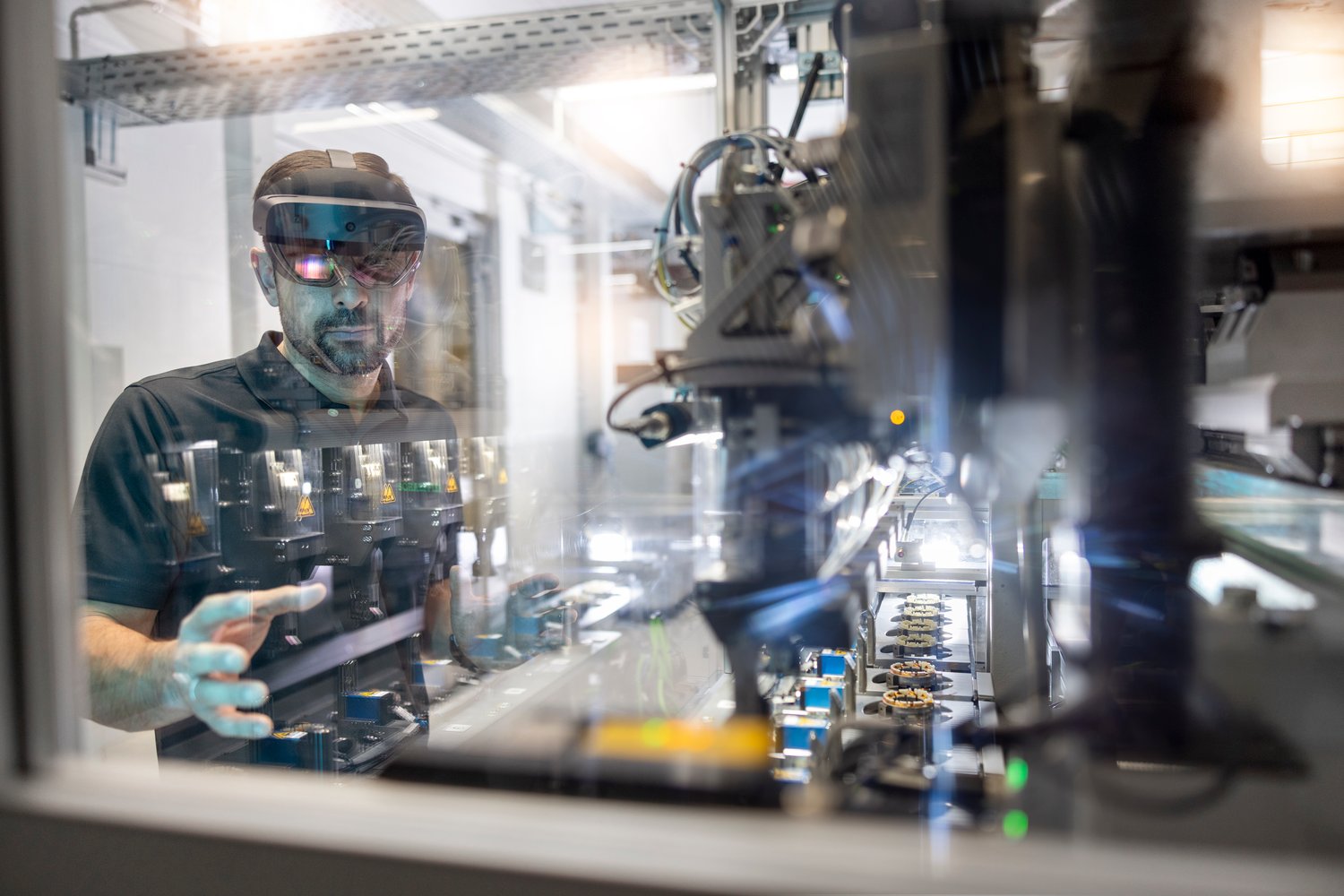
Optimize your production design with Special Machinery
At Special Machinery, we are happy to help you optimize your production design. We analyze your specific requirements and identify areas for improvement. Based on this analysis, we develop a tailor-made concept for you, including a turnkey solution for series production that is implemented directly at your site.
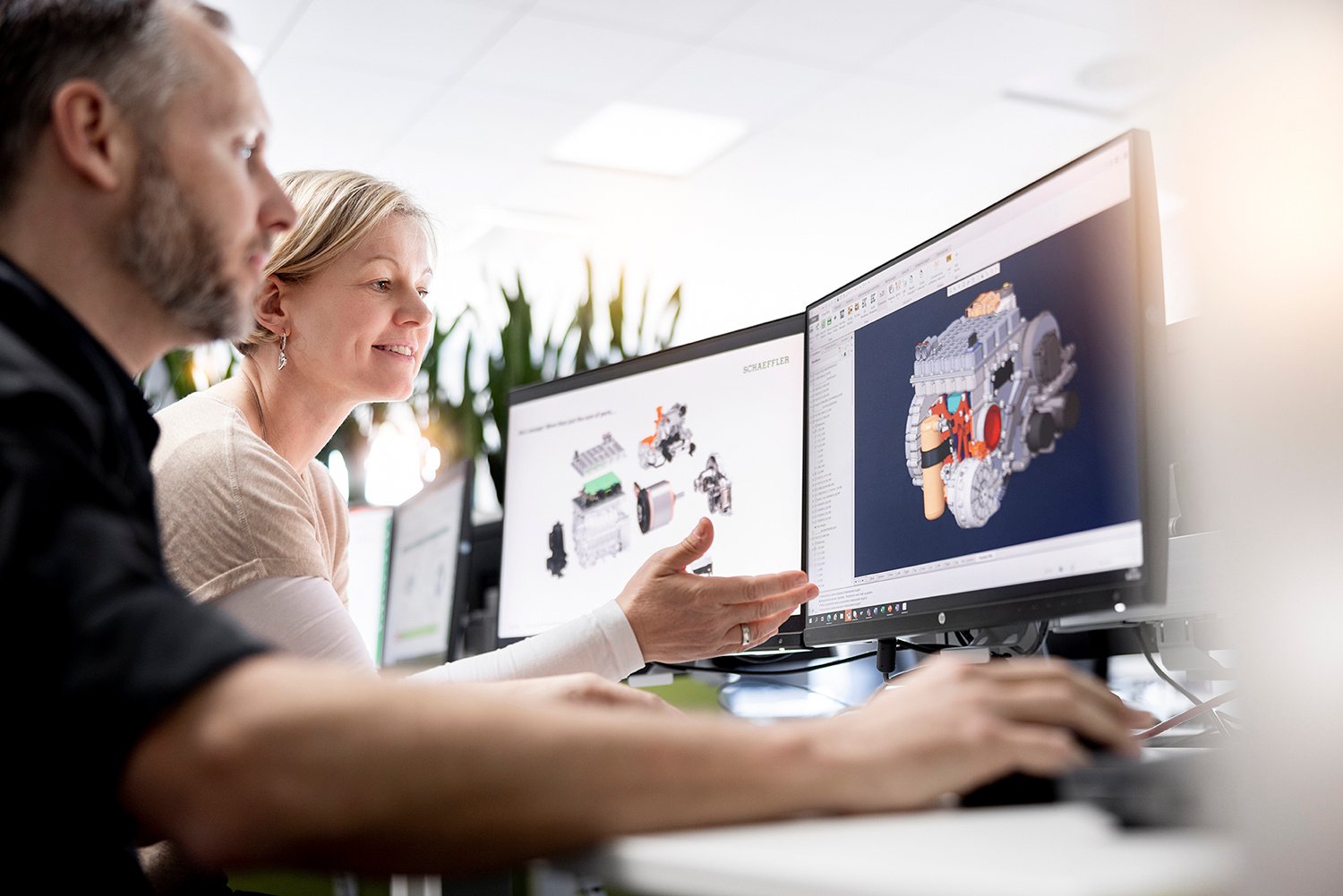
Our experts design seamless integration
Our skilled engineers create processes and systems that integrate smoothly with your current value chain. We consider multiple factors that could impact your project, including the product's development stage, industrialization planning, and related costs.
The road to manufacturing excellence
With Special Machinery as your partner, you can count on getting a production solution that:
Advanced and efficient
Processes designed to maximize your productivity.Perfectly connected
Seamless integration on your existing infrastructure and systems.Cost-saving
Solutions designed to reduce your total cost of ownership.Future-proof
Technology that can be scaled to suit your changing needs.Projects we are proud of
With Speciale Machinery as your partner, you can count on getting a production solution that suits your needs and requirements.
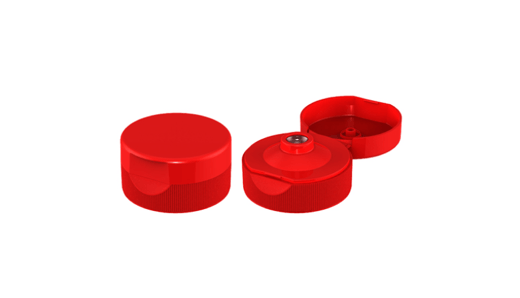
Assembly of dosing caps
View project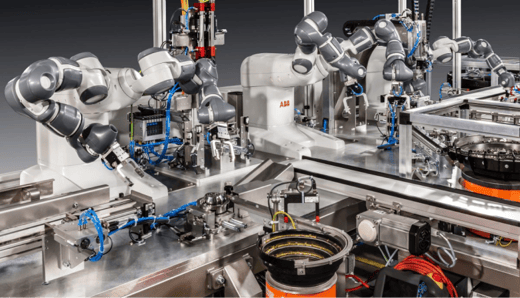
Assembly of ABB hollow wall boxes and ring
View projectAssembly of ABB hollow wall boxes and ring
- Handling with 3 Yumi robots.
- 6 bowl feeders for the supply of the components.
- Processes: including screws, placing clips and placing pull strips.
- Performance: 20 pieces / minute.
- Assembly and packaging of box or ring (assembly of 2 types of products integrated in 1 machine)
- Worldwide the first implementation of 3 Yumi robots in an assembly line.
- Click here for the impression video of ABB itself.
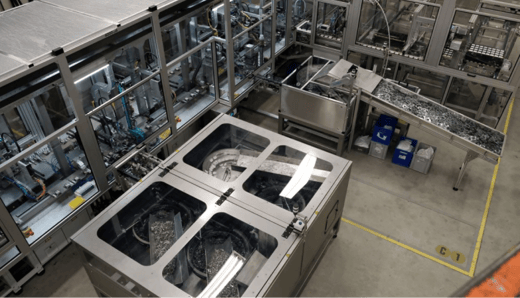
Assembly of powersockets
View project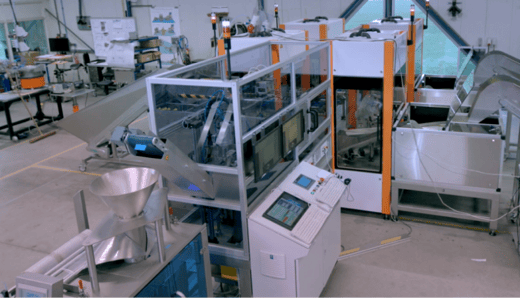
Laser coding and RFID programming ear tags
View projectLaser coding and RFID programming ear tags
- Feeding of ear tags by four Radiflex robot vision feeding systems.
- 6-axis Epson robots.
- Conveyor tracking (vision) combined with a universal bowlfeeder.
- Programming of the RFID chip.
- reading chip.
- Laser coding.
- Packaging of sets.
- > 30 different ear tags in size and shape
- Performance: 4 x 20 pieces / minute.
- Click here for the video of the machine in production.
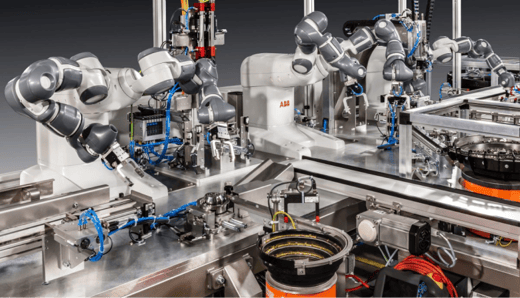
Assembly of ABB hollow wall boxes and ring
View projectAssembly of ABB hollow wall boxes and ring
- Handling with 3 Yumi robots.
- 6 bowl feeders for the supply of the components.
- Processes: including screws, placing clips and placing pull strips.
- Performance: 20 pieces / minute.
- Assembly and packaging of box or ring (assembly of 2 types of products integrated in 1 machine)
- Worldwide the first implementation of 3 Yumi robots in an assembly line.
- Click here for the impression video of ABB itself.
If the solution you're looking for isn't listed, please get in touch with us. We're happy to collaborate and find the right solution for you.
Contact usThe benefits of
Manual versus automated production: Make the switch to excellence
Why choose automated production?
Moving from manual to automated production offers a range of benefits that take your efficiency, quality and profitability to the next level.
Discover the transformative power of automation.
- Automated processes eliminate human error, resulting in consistent, high-quality output.
- Reduce waste and save on rework costs through accurate, repetitive processes.
-
Adjust your production effortlessly with automated systems that seamlessly match your changing demand.
-
Increase or decrease your capacity quickly and efficiently to meet peak demand or seasonal fluctuations.
- Decouple your production from labour market tightness. Automated systems ensure continuous production regardless of staff availability.
- Reduce your costs and increase your flexibility with a reliable, robotised workforce.
-
Plan with certainty thanks to constant production capacity. Forecast production volumes accurately and meet deadlines without stress.
-
Increase customer satisfaction through on-time deliveries and eliminate delays due to unforeseen factors.
- Experience unparalleled consistency in your products. Automated processes with integrated checkpoints ensure top quality in every production.
- Reduce return rates and increase customer satisfaction with products that meet the highest standards.
Types of machine construction
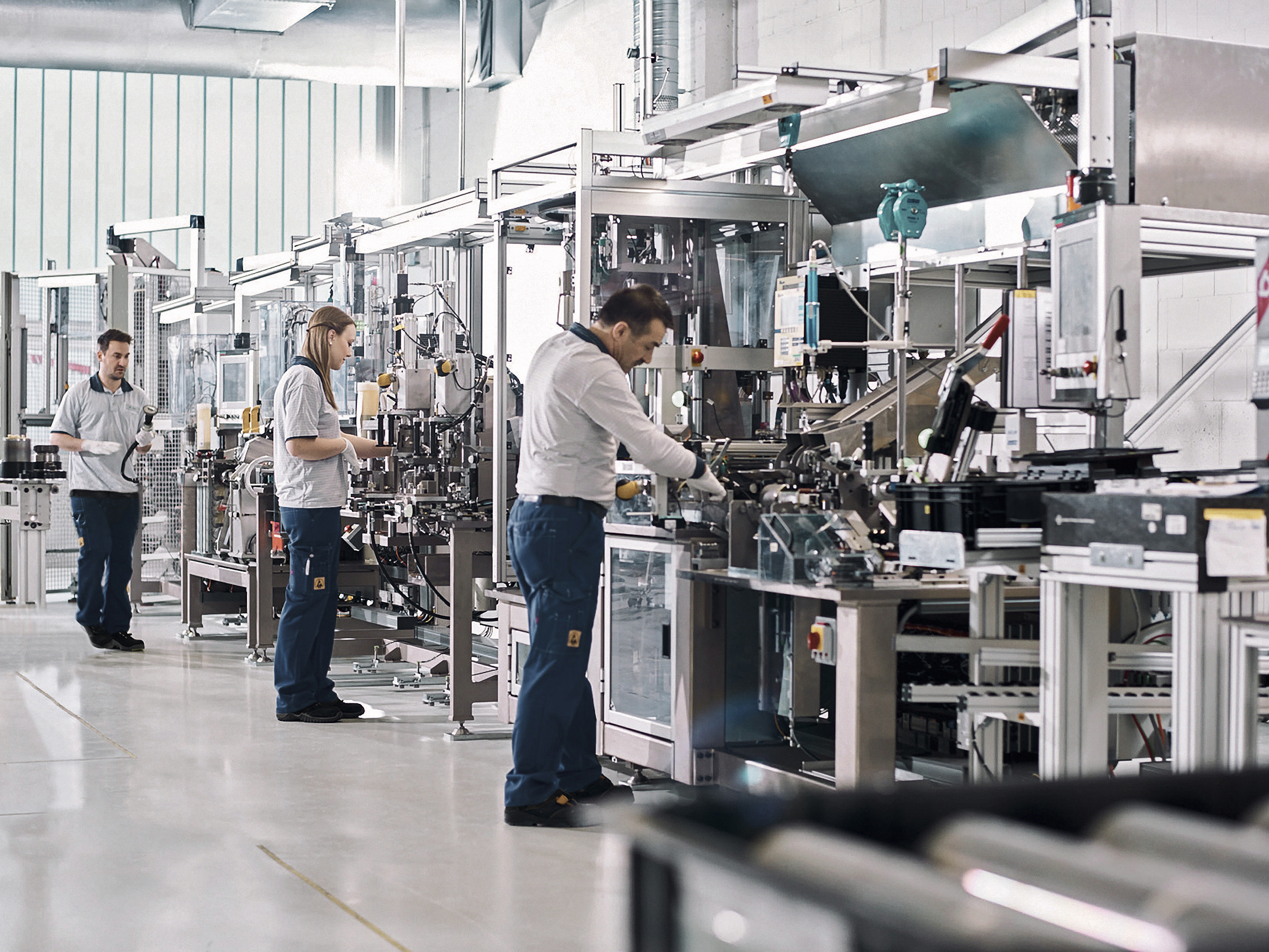
Series production
Series production offers an efficient, consistent, and cost-effective solution for manufacturing.
How does it work?
01
Analysis current situation
02
Testing of possible outputs
03
Draft proposal machine
04
Design phase
05
Build phase
06
Test phase - Factory Acceptance Testing (FAT)
07
Implementation + Site Acceptance Test (SAT)
08
After-sales service
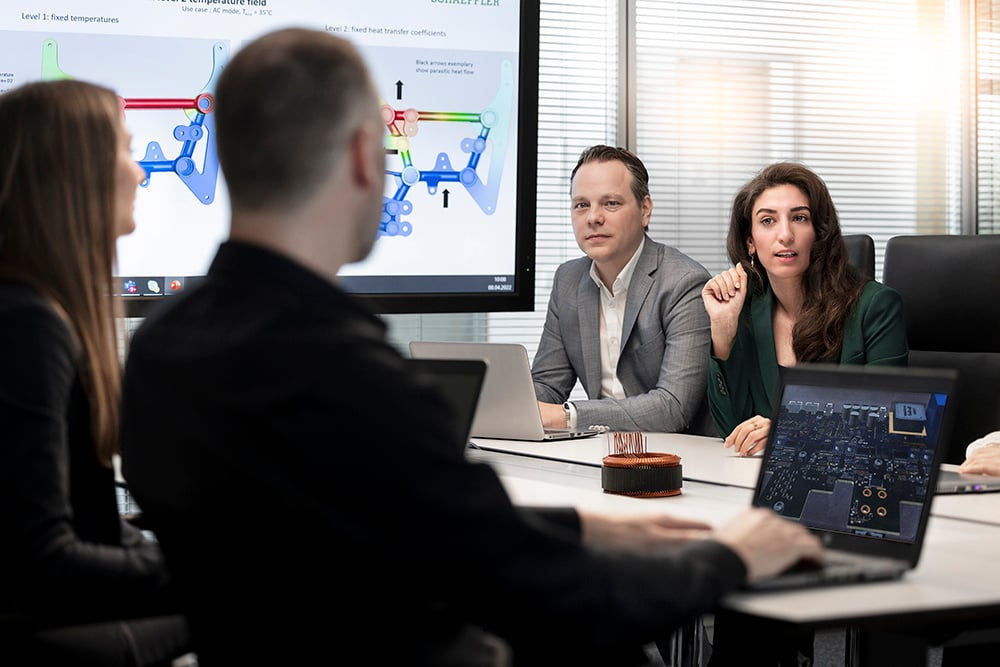
More information about your project
UploadSchedule an appointment
Contact one of our technical advisers.